O NAMA
IGM MLADOST je jedan od najvećih i najznačajnijih proizvođača građevinskog materijala u regionu, sa tradicijom dugom preko 113 godina. Poznato ime na tržištu, sinonim za kvalitetne crepove i blokove za zidanje i međuspratne konstrukcije koji su pored prisustva na domaćem tržištu, zahvaljujući kvalitetu, pronašli put do zadovoljnih korisnika na mnogim tržištima: Makedoniji, Bugarskoj, Rumuniji, Albaniji, Bosni i Hercegovini, Slovačkoj, Crnoj Gori, Rusiji, Poljskoj, Nemačkoj, Francuskoj i Belgiji.
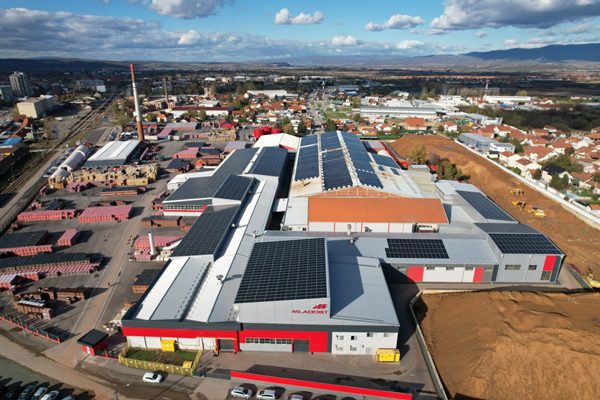
IGM Mladost – Leskovac
Kroz istoriju, "Keramička fabrika Rafajlović, Sokolović i Bejaž", kasnije poznata kao "MLADOST", postala je sinonim za vrhunski građevinski materijal od gline. 🧱
Na temeljima stare ciglane, sa simboličnim dimnjakom koji dominira Leskovcem, nastali su prepoznatljivi crepovi s utisnutim znakom slona i živopisnom crvenom bojom.
Od tradicionalnih metoda do modernizacije 1974. godine, naša fabrika nastojala je očuvanju kvaliteta i stručnosti u svakom koraku. Usledio je period stabilnosti i umerenog razvoja, sve dok nismo postali akcionarsko društvo 2003. godine, podstaknuti željom za inovacijama.
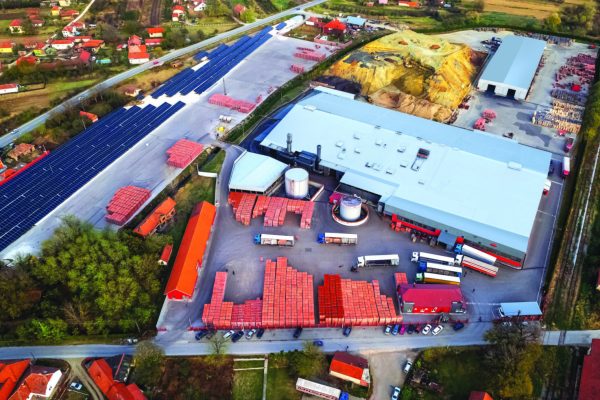
IGM MLADOST d.o.o. Leskovac – ogranak Mala Plana
Od 2007. do 2010., uložili smo značajna sredstva u tri fabrike - Leskovcu, Vlasotincu i Maloj Plani. Težili smo najnovijoj tehnologiji, unapređenju infrastrukture, optimizaciji procesa i osnaživanju naših ljudskih resursa!
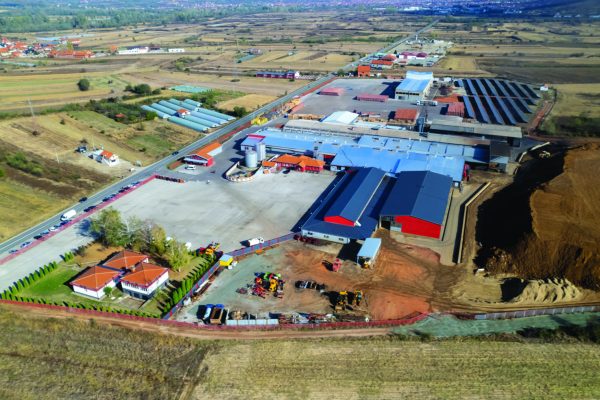
IGM MLADOST d.o.o. Leskovac – ogranak Vlasotince
Pre privatizacije, fabrika u Vlasotincu proizvodila je blokovsku robu i crep za lokalno tržište. 2006. godine donela je velike promene - privatizacija je započela novu eru za nas! 2008. godine sprovedena je rekonstrukcija koja je postavila osnove za naš tehnološki napredak. Fabrika je postala tehnički savremena, automatizovana i robotizovana, što nam je omogućilo da zadovoljimo sve zahteve tržišta i potrebe kupaca. Investicije su bile značajne - potpuno nova proizvodna linija, novi mlinovi, presa najnovije generacije, roboti i potpuna automatizacija procesa sušenja i oblikovanja robe. Rezultat svega ovoga? Danas ponosno proizvodimo različite vrste građevinskog materijala, kao što su giter 5, energetske blokove za spoljne i unutrašnje zidove, termoblokove različitih dimenzija, fert i ventilacione blokove.
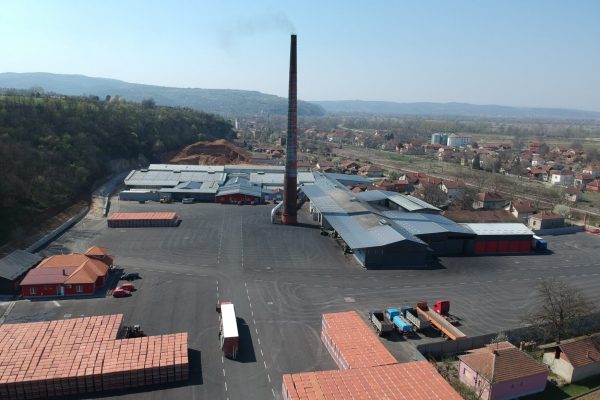
IGM MLADOST d.o.o. Leskovac – ogranak Stalać
Sa poslednjom investicijom s kraja 2010. i početka 2011. godine, kao i sa rekonstrukcijom nove fabrike u Stalaću početkom 2018. godine, investicioni ciklus je krunisan instaliranjem ključnih tehnologija koje će omogućiti značajno poboljšanje kvaliteta, kvantiteta i asortimana proizvodnje, a sve u cilju zadovoljenja potreba naših kupaca.
Industrija građevinskog materijala IGM MLADOST objedinjuje pet fabrika u centralnoj i južnoj Srbiji u jedno prepoznatljivo ime znano, pre svega, po kvalitetu svojih proizvoda. U fabrici u Leskovcu organizovana je proizvodnja crepa, dok se u fabrikama u Topličkoj Maloj Plani, Vlasotincu i Stalaću proizvodi blokovska roba za zidanje i međuspratne konstrukcije. Svoj veliki ugled MLADOST temelji na preko sto godina dugoj tradiciji. Naime, osnivanjem naše prve fabrike za proizvodnju keramičkih proizvoda 1911. godine postavljeni su temelji savremene proizvodnje građevinskog materijala od gline. Najviši dimnjak u Leskovcu nalazi se upravo u ovoj fabrici i simbol je tradicije i svedočanstvo umeća, postojanosti i lepote graditeljskog stvaranja.
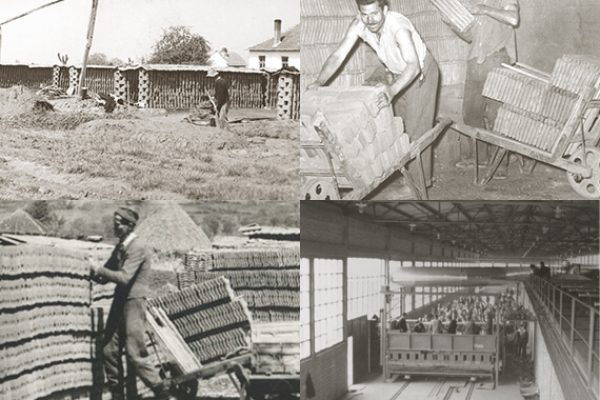
Početak Našeg Uspeha
Proizvodnja građevinskog materijala od gline u okolini Leskovca, Vlasotinca i u slivu Toplice, stara je koliko i prisustvo ljudskih zajednica na tom prostoru. Izobilje kvalitetne sirovine koristili su neimari drevnih carstava ostavivši spomenike svog graditeljskog umeća. Na prelazu između antike i srednjeg veka, nastao je Caričin grad kod Lebana, najstariji spomenik arhitekture na prostoru južne Srbije. Tradicija proizvodnje opeke iz Vizantijskog doba nastavlja se i u srednjem veku, u kome nastaju mnoga dela sakralne arhitekture, prvenstveno u slivu Toplice.
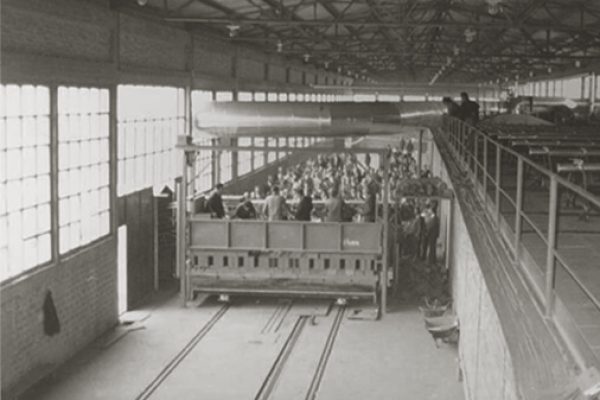
Početak Našeg Uspeha
Od tih davnih vremena pa do danas, dešavale su se promene u vlasništvu i organizaciji ali ne i promene u veštini izrade proizvoda od gline, koja se kao i prepoznatljiva crvena boja, pokazala trajnijom od mnogih društvenih sistema i epoha. Upravo na temeljima ovako duge i bogate tradicije u proizvodnji keramičkih proizvoda u ovim krajevima, na najatraktivnijim lokacijama, nastale su i naše fabrike u Leskovcu, Vlasotincu, Topličkoj Maloj Plani i Stalaću.
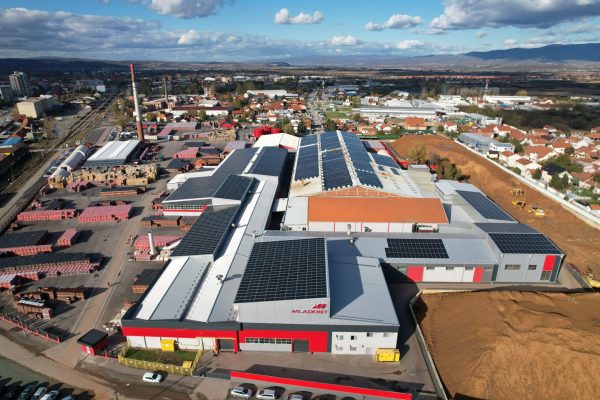
Mladost Danas
Zahvaljujući idealnom mineraloškom sastavu sirovine, svi proizvodi, osim izuzetnih fizičko-mehaničkih karakteristika, imaju intenzivnu i trajnu crvenu boju po kojoj se upadljivo razlikuju od svih drugih proizvoda ove vrste. Zbog ovakvih svojstava, svi naši proizvodi su ubrzano osvojili mnoga tržišta. Bez proizvoda proizvedenih u fabrikama MLADOST, danas se gotovo ne može zamisliti savremena gradnja u Srbiji i širem regionu.
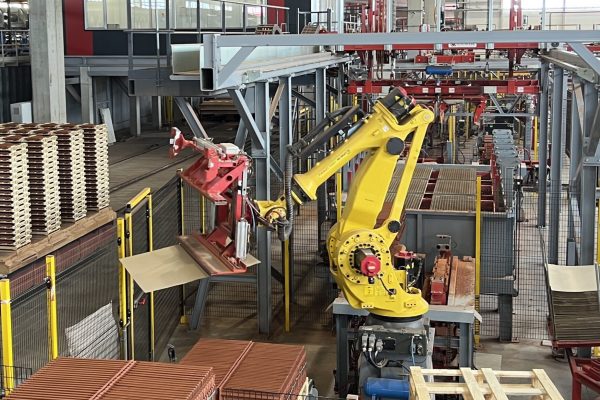
Mladost Danas
Danas su to izuzetno moderne fabrike. Velikim investicionim ulaganjima, u svim fabrikama uvedena je najsvremenija oprema i tehnologija koja, zajedno sa izuzetno kvalitetnom sirovinom i stručnom radnom snagom, omogućava proizvodnju koja zadovoljava najstrožije zahteve za kvalitetnom, ekonomičnom i jednostavnom gradnjom.
Mladost - kvalitet koji se nasleđuje
MLADOST je jedan od najvećih i najznačajnijih proizvođača građevinskog materijala u regionu Balkana i jugoistočne Evrope. Sinonim je za kvalitetne crepove, blokove za zidanje i međuspratne konstrukcije. MLADOST – sistem za savremenu gradnju!
Evo kako smo krenuli…
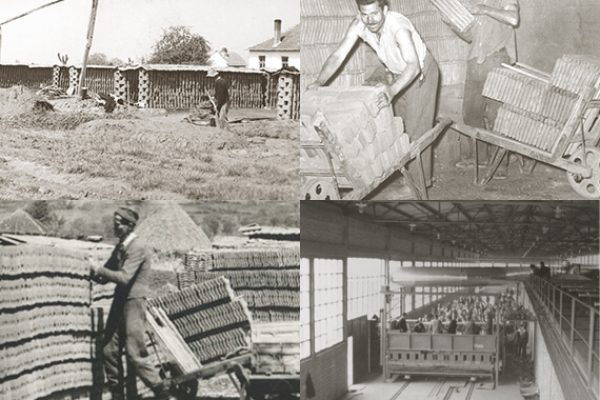
IGM MLADOST Leskovac
1911. godina
1911. godina – osnivanjem “Keramičke fabrike Rafajlović, Sokolović i Bejaz” postavljeni su temelji savremene industrije građevinskog materijala od gline. Ogromna zgrada takozvane “stare ciglane” sa najvišim dimnjakom u Leskovcu i danas predstavlja jedan od simbola grada. Crep koji se početkom prošlog veka proizvodio u Leskovcu, sa utisnutim znakom slona i svojom prepoznatljivom, intenzivnom crvenom bojom i danas krasi krovove Leskovca, Niša, Vranja, Skoplja i mnogih bližih i daljih gradova.
Tradicionalne metode oblikovanja gline primenjivane su sve do 1974. kad je izgrađena nova hala sa uređajima i mašinama za proizvodnju crepa i blokovske robe, savremenim za taj period istorije. Međutim, pojedini segmenti tadašnje proizvodnje su se i dalje zasnivali na ručnom radu i primeni velikog broja radnika, bez detaljnog sagledavanja mogućnosti povećanja kvaliteta i kvantiteta proizvodnje.
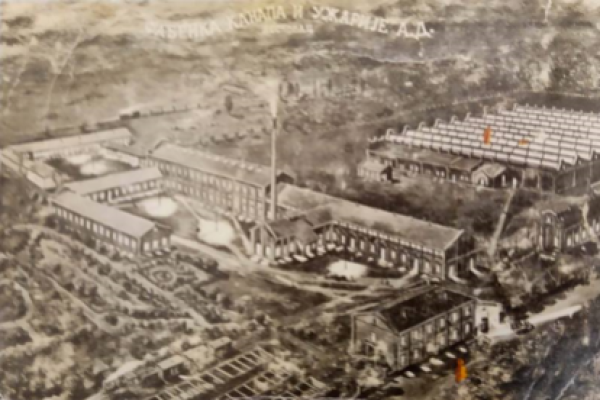
IGM MLADOST Leskovac
DP Pobeda
1928. godina– istupanjem iz zajednice jednog od vlasnika Mihajla Sokolovića, fabrika dobija nov naziv “Keramička fabrika Rafajlović i Bejaz”. Nakon Drugog svetskog rata fabrika prerasta u DP “Pobeda” – Industrijsko preduzeće crepa i cigle, čiji će proizvodi biti poznati širom stare Jugoslavije.
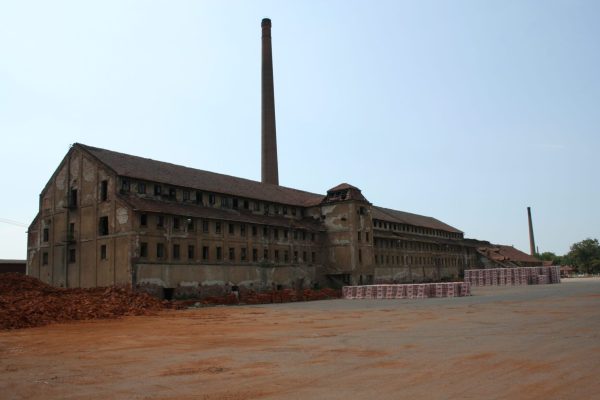
IGM MLADOST Leskovac
DP Mladost
1997. godina – izvršena je podela preduzeća na više manjih, specijalizovanih za proizvodnju pojedinih vrsta građevinskog materijala. Tako nastaje D.P. “MLADOST” kao skup mladih, vrednih i motivisanih ljudi, koji žele da se vrate na svoja stara tržišta i da se predstave novim. Period koji je tada nastupio je obeležen stabilnošću u poslovanju i umerenim razvojem, u skladu sa opštim okolnostima u društvu. 2003. godina – privatizacijom preduzeća MLADOST postaje akcionarsko društvo, a poslovodstvo i zaposleni dobijaju novi podstrek za dalje unapređenje i razvoj. Od tog momenta pa sve do 2008. godine radilo se na konstanom povećavanju kvaliteta i kapaciteta proizvodnje, a firma IGM MLADOST se u potpunosti preorijentisala na proizvodnju crepa. U istom periodu, kompanija je iskoristila vreme za zapošljavanje i stručno usavršavanje novih kadrova osnovnih proizvodnih profila: tehnologija, mašinstvo i elektronika.
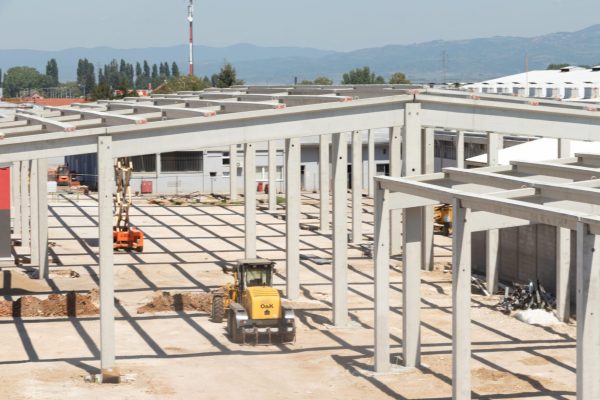
IGM MLADOST Leskovac
RAST i RAZVOJ FABRIKE
2008. godina – počinje novo razdoblje rekontrukcijom fabrike koja predstavlja bitan korak u osavremenjavanju procesa proizvodnje naročito u delu primarne prerade, uvođenjem najsavremenijih mlinova velikog kapaciteta za finu preradu gline, kao i veliki napredak u slaganju i razlaganju suve i pečene robe a naraočito u pogledu pakovanja proizvoda uz potpunu automatizaciju procesa. Takođe, veliki akcenat tokom prve faze rekonstrukcije je dat na osavremenjavanju i automatizaciji procesa sušenja i pečenja proizvoda, i to sa najsavremenijim sistemima za praćenje i kontrolu kvaliteta procesa. Uz to u velikoj meri doprineseno je povećanju kvaliteta uslova rada i humanizaciji posla.
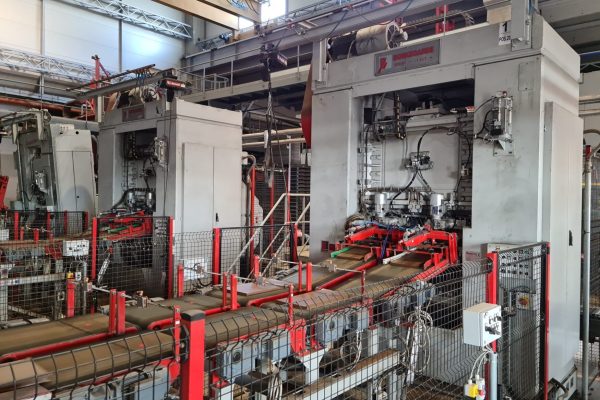
IGM MLADOST Leskovac
RAST i RAZVOJ FABRIKE
2011. godina– drugi deo ove rekonstrukcije sa dogradnjom proizvodne hale sirove proizvodnje koja se zasniva na postavljanju novog ekstrudera nemackog proizvodjaca “Händle” i instalaciji novih dvoglavih presa italijanske firme “Bongioanni” koje spadaju u red najsavremenijih u ovoj oblasti. Primena ove savremene i visoko kontrolisane tehnologije, direktno utiče na kvalitet proizvoda u pogledu fizičko mehaničkih karakteristika, kao in a estetski izgled crepa čime se zadovoljavaju zahtevi sve probirljivijeg tržišta.
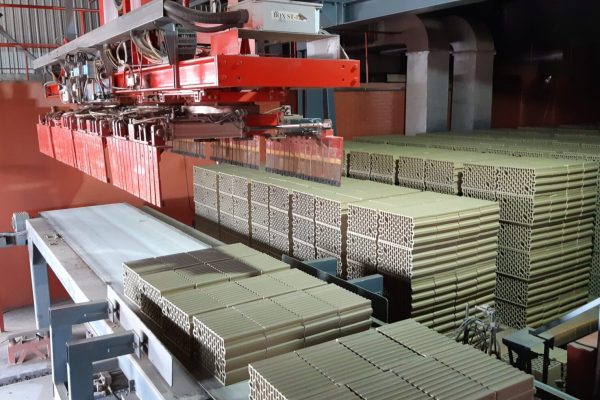
IGM Mladost Mala Plana
2006. godina izvršena je privatizacija fabrike IGM “7. JULI” u topličkoj Maloj Plani koja je do tada poslovala kao društveno preduzeće. Od tog dana fabrika posluje pod imenom IGM “MLADOST-TMP” d.o.o. Odmah nakon privatizacije, već tokom 2006.godine krenulo se u rekonstrukciju fabrike: 2007. godine ugrađena je kompletno automatska linija slaganja i razlaganja proizvoda, ugrađen je potpuno novi fini mlin renomiranog nemačkog proizvođaca Haendle, izvršena je rekonstrukcija peći i ugradnja novih gorioničkih grupa. Instaliran je sistem za nadzor temperature i ostalih parametara u peći i sušari, 6 ventilatorskih grupa za sušaru, kompresor visokog pritiska i urađena nova mreža za razvod komprimovanog vazduha. Izgrađena je i nova proizvodna hala za potrebe smeštaja opreme za razlaganje proizvoda.
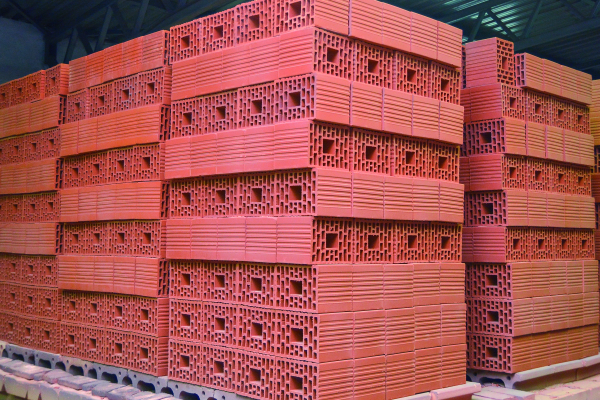
IGM Mladost Mala Plana
2008. godina izvršena je rekonstrukcija linije oblikovanja, prerađena je presa na sistem sa dva izlaza i ugrađena je odgovarajuća automatika za utovar sirovih proizvoda na vagone sušare. Povećan je broj ventilatoriskih grupa u sušari i izvršena je automatizacija kompletne linije oblikovanja, utovara sirove robe i istovara suve robe. Ugrađen je kolni mlin većeg kapaciteta, zatim jos jedan kompresor visokog pritiska kao i novi trafo od 630 kW.
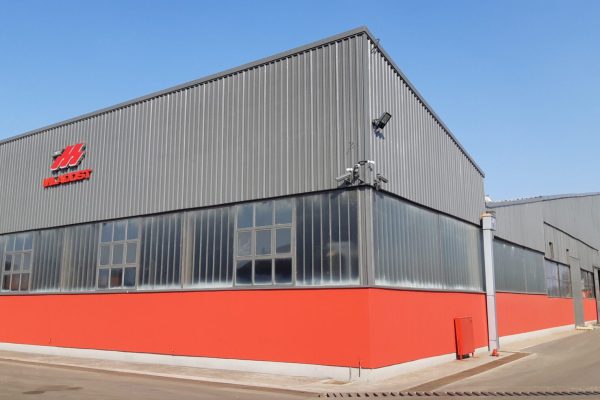
IGM Mladost Mala Plana
2009-2010. godina – ugrađena je sledeća oprema: grubi mlin Bedeschi, ekstruder Bedeschi, ventilator dimnih gasova, sistem za recirkulaciju dimnih gasova na peći. Izvršena je rekonstrukcija primarne prerade.
Sve ove investicije i tehničko tehnološki zahvati, omogućili su proizvodnju izuzetno kvalitetnih proizvoda uz istovremeno povećanje kapaciteta, zbog čega se IGM MLADOST-TMP ubraja u najveće proizvođače blokovske robe u Srbiji.
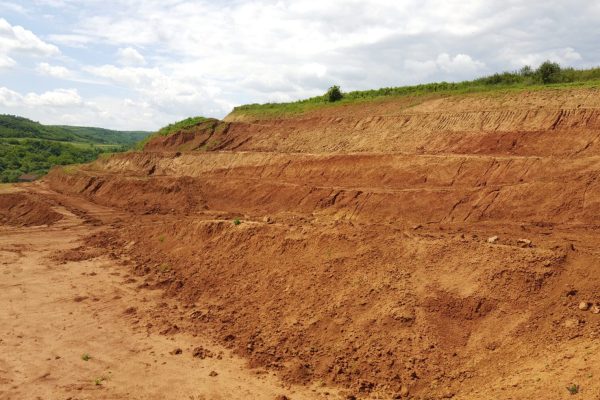
IGM Mladost Mala Plana
2010. godine otvoren je novi kop veoma kvalitetne gline koji omogućava pravilan pristup eksploataciji sa odgovarajućom pristupnom saobraćajnicom za nesmetano odvijanje transporta. Izgrađen je novi rezervoar za mazut od 1.000 m3 i izvršeno asfaltiranje 10.000 m3 prostora za skladištenje gotovih proizvoda; izgrađena je nova upravna zgrada, renovirane prostorije tehničkih službi i restoran za ishranu radnika unutar proizvodne hale.
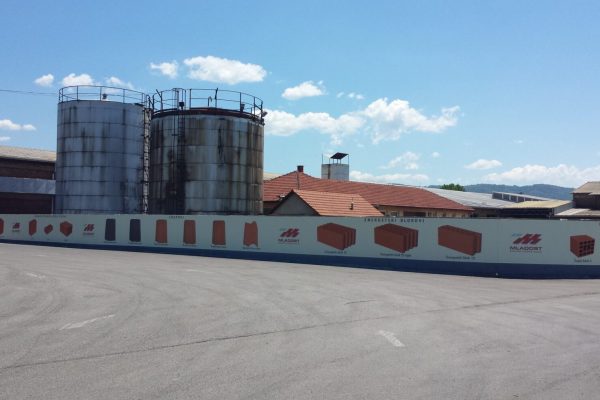
IGM Mladost Vlasotince
Fabrika IGM “RAD” u Vlasotincu je poslovala kao društveno preduzeće sve do 06.11.2006. godine kada je izvršena privatizacija , i od tog dana fabrika posluje pod imenom IGM “MLADOST RAD” AD.
U periodu pre privatizacije fabrika je proizvodila blokovsku robu (oko 5.500.000 komada na godišnjem nivou) i crep (oko 2.000.000 komada) koje je uglavnom plasirala na lokalnom tržištu.
2007. godina – počinju pripreme za rekonstrukciju fabrike, a s ciljem da se proizvodnja unapredi i značajno osavremeni.
2008. godina – obavljena rekontrukcija
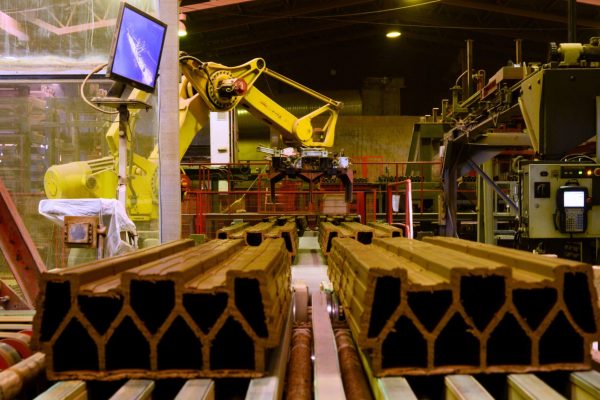
IGM Mladost Vlasotince
2009. godina – početak proizvodnje po novoj tehnologiji.
Ovom rekontrukcijom fabrika je postal tehnološki savremena, automatizovana i robotizovana sto je bio uslov za proizvodnju građevinskog materijala u skladu sa tržišnim zahtevima i potrebama kupaca.
Konkretni investicioni poduhvati su bili: potpuno nova proizvodna linija, novi mlinovi primarne i sekundarne prerade proizvođača “BONGIOANNI”, presa najnovije generacije proizvođača “BEDESCHI”, roboti najnovije generacije japanskog proizvođača “FANUK”, kompletno automatizovan proces linije sirovog oblikovanja, suvog slaganja robe na vagonima i linija za razlaganje pečene proizvodnje, kompletno rekonstruisane i osavremenjene sušare.
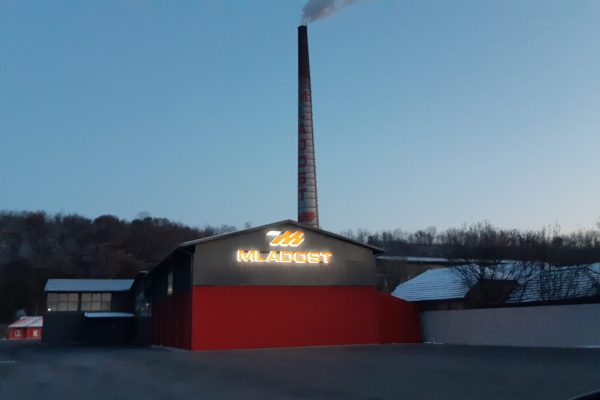
IGM Mladost Stalać
Preduzeće „Vojvoda Prijezda“ Stalać radi od 1948. godine, pa je to i godina kada zvanično počinje proizvodnja ciglarskih proizvoda. Osnovna delatnost preduzeća je proizvodnja i podaja građevinskog materijala (opeka i crepa od gline). U periodu od 1948. od kada preduzeće počinje da radi, pa do 2006. godine od kada se registruje kao Akcionarsko društvo „Vojvoda Prijezda“ za proizvodnju i prodaju građevinskog materijala Stalać, dogodile su se sledeće organizacione i statusne promene: • Preduzeće je do 1953. godine bilo samostalno, da bi pomenute godine prešlo u sastav preduzeća „Dušan Ristić“ iz Kruševca, gde posluje kao radna jedinica. • 1973. godine preduzeće postaje OOUR „Stalać“ u okviru RO „Dušan Ristić“ iz Kruševca. • 1989. godine preduzeće se izdvojilo iz sastava RO „Dušan Ristić“ iz Kruševca i od tada posluje pod imenom
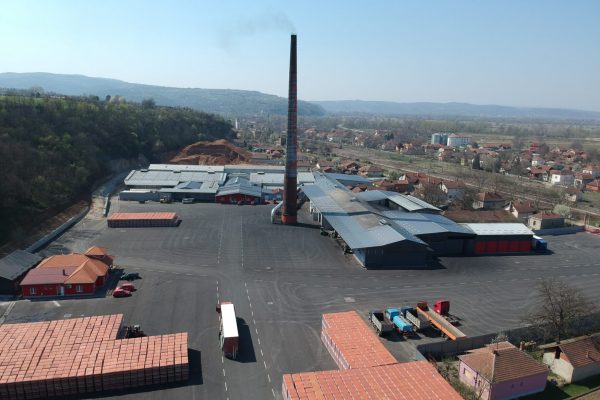
IGM Mladost Stalać
Deoničarsko društvo „Vojvoda Prijezda“, Stalać kao posebno pravno lice. • 2002. godine rešenjem Trgovinskog suda u Kraljevu, a radi usklađivanja delatnosti sa Zakonom o klasifikaciji delatnosti, preduzeće posluje pod nazivom Društveno preduzeće za proizvodnju i prodaju građevinskog materijala „Vojvoda Prijezda“, Stalać. • 2005 godine aukcijskom prodajom 06.10.2005. god. Preduzeće menja oblik svojine i prelazi u A.D. „Vojvoda Prijezda“ sa 70 % prodatog kapitala. • 2007. godine po Zahtevu za prinudnu prodaju „Mašinac” d.o.o. Kraljevo otkupljuje i preostalih 30% kapitala. Osnovna delatnost preduzeća je proizvodnja i prodaja građevinskog materijala, a preduzeće je registrovano za obavljanje i drugih delatnosti, koje su navedene u sudskom registru, kao i za poslove spoljnotrgovinskog prometa koji se obavljaju u okviru upisane delatnosti trgovine na veliko. 30.06. 2017 godine „Vojvodu Prijezdu“ iz stečaja kupuje kompanija „Mladost“ Leskovac i do 31.12.2023. godine posluje samostalno pod nazivom „Mladost -
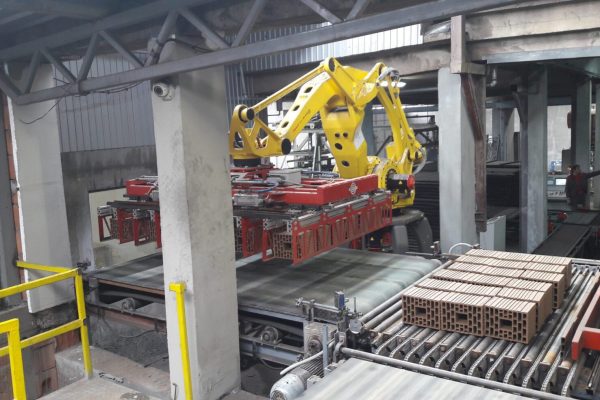
IGM Mladost Stalać
Vojvoda Prijezda“ Stalać, da bi se po Odluci o pripajanju od 01.01.2018. u kompaniju „Mladost“ doo Leskovac kao Ogranak Stalać. Rekonstruikcija fabrike je otpočela je od 31.08.2017.godine, po svim pozicijama i sa proizvodnjom krenulo 19.03.2018. godine, cela kalendarska godina kao i 2019 godina se radilo na investicionom ulaganju i povećanjem kapaciteta proizvodnje. Danas se u proizvodnom pogonu Stalać proizvode široka paleta Mladost energetskih blokova, termobloka kao i standardnih blokova. Koristeći najsavremeniju tehnologiju i znanje najboljih stručnjaka na tom području, Mladost energetski glineni blokovi omogućavaju energetsku efikasnost objekata u koji su ugrađeni. Oni su moderno i ekološko rešenje koje garantuje postojanost i dugotrajnost, zdravu prostornu mikroklimu i siguran dom za buduće generacije.
U našim fabrikama se koristi izuzetno kvalitetna glina koja je bila predmet ispitivanja Instituta za istraživanje materijala iz Beograda.
IZVOD IZ NAUČNOG RADA
“OCENA KVALITETA OPEKARSKIH SIROVINA SA JUGA SRBIJE”
Dr Zagorka Radojević,dipl.ing., Milica Arsenović,dipl.ing.tehnol., Miloš Vasić,dipl.ing.tehnol.
U radu su prikazani rezultati istraživanja kvaliteta tri opekarske sirovine sa juga Srbije: sa ležišta kod Leskovca, sa ležišta kod Vlasotinaca i sa ležišta kod Male Plane. Istraživanja su obuhvatila hemijske, mineraloške, granulometrijske i keramičko-tehnološke karakteristike reprezentativnih uzoraka sa navedenih ležišta. U radu je data i ocena sirovina sa aspekta kvaliteta opekarskih proizvoda, energetske efikasnosti i ekoloških parametara.
Uvod
Osnovne sirovine za proizvodnju opekarskih proizvoda su gline, les, glinci, laporci i dr. Geološka istraživanja i ispitivanja sirovina u Srbiji obavljaju se na jedinstven način. Ova istraživanja vrše se po opšte važećim metodama i propisima, koji pružaju dovoljno podataka o kvalitetu i količinama sirovine i na osnovu kojih se donosi odluka o eksploataciji. Ne postoji građevinski materijal koji bi mogao da zameni opekarske proizvode u pogledu čvrstoće, poroznosti, izolacionih sposobnosti, postojanosti, sigurnosti protiv požara, otpornosti na atmosferilije i koroziju, postojanosti oblika i mogućnosti za ostvarenje raznolikosti pri gradnji. Pored navedenih pozitivnih osobina ovog građevinskog materijala, na proizvodnju i upotrebu opekarskih proizvoda upućuje i sve urgentnija potreba za očuvanjem okoline, a s tim i očuvanje uslova za život, rad i zdravlje ljudi. Jug Srbije ima razvijenu proizvodnju različitih asortimana opekarskih proizvoda. U pogonima za proizvodnju opekarskih proizvoda: “MLADOST” d.o.o. – Leskovac, “MLADOST-RAD” d.o.o. – Vlasotince i “MLADOST-TMP” – Mala Plana, puštene su u rad savremene visoko automatizovane tehnološke linije. Njihov rad je oslonjen nakvalitetnu lokalnu sirovinsku bazu. U radu je data ocena sirovina sa aspekta kvaliteta proizvoda, energetske efikasnosti i ekoloških parametara.
KVALITET OPEKARSKIH PROIZVODA
Na osnovu rezultata ispitivanja opekarskih sirovina sa juga Srbije može se zaključiti da se savremenom proizvodnjom mogu dobiti: Opekarski proizvodi široke lepeze asortimana (crep, fasadna opeka i blokovi, opekarski proizvodi za unutrašnji ozid, tavanični elementi, porozirani opekarski proizvodi i dr.
Proizvodi visokih estetskih svojstava, intenzivno crvene boje,
Proizvodi bez iscvetavanja soli i defekata dejstva kreča,
Proizvodi visokih mehaničkih karakteristika (pritisna i savojna čvrstoća),
Proizvodi koji obezbedjuju dobru otpornost na požar i odlična termička i akustična svojstva objekata.
Boja pečenih opekarskih proizvoda u osnovi zavisi od mineraloškog sastava sirovine, temperature i uslova pečenja. Dominantan uticaj na boju opekarskih proizvoda ima gvožđe. Opekarske sirovine sadrže gvožđe uglavnom u obliku minerala iz grupe hidroksida (getit, limonit).U procesu pečenja hidroksid gvožđa se transformiše u hematit, koji keramičkom telu daje crvenu boju. Iz rezultata ispitivanja zaključuje se da je boja pečenih proizvoda intenzivno crvena.
Nizak sadržaj ili odsustvo karbonata ukazuju na odsustvo štetnog dejstva kreča na pečenim proizvodima.
Mehaničke karakteristike pečenih proizvoda su visoke.
ENERGETSKA EFIKASNOST
Rezultati ispitivanja keramičko-tehnoloških karakteristika uzoraka ukazuju da je zahtevana temperatura pečenja relativno niska, 830-9000C.Niska temperatura pečenja značajno snižava specifičnu potrošnju energije u procesu pečenja i povećava energetsku efikasnost procesa. Radi poređenja najčešće je zahtevana temperatura pečenja za opekarske proizvode u pogonima u Srbiji u intervalu 950-10500C. Dobra plastičnost ispitivanih uzoraka omogućuje proizvodnju opekarskih proizvoda tanjih zidova, odnosno manje mase što smanjuje potrošnju sirovine i utrošak energije po jedinici normalnog formata.
EKOLOŠKI ASPEKT
Izbegavanje zagađivanja životne sredine se postavlja pred savremene procese proizvodnje.Proizvodnja opekarskih proizvoda dozvoljava primenu otpadnih materijala. Ispitivane sirovine se mogu umešavati sa otpadnim materijalima uz projektovanje optimalnih mešavina za određenu vrstu proizvoda. Emisija gasova u procesu pečenja dolazi iz goriva i iz sirovine. Tako se pojavljuju HF, SO3, SO2, HCl, CO2 i dr. Ova problematika traži ozbiljna izučavanja sveukupne emisije i neophodnih mera.
Međutim, na bazi rezultata ispitivanja hemijskog sastava sirovina sa juga Srbije nema uslova za značajniju emisiju, jer je sadržaj komponenti koje emituju štetne gasove u procesu pečenja minimalan ili ih nema. Čak je i sadržaj karbonata u sirovini nizak, pa gotovo da nema emisije CO2 koji potiče iz sirovine.
ZAKLJUČAK
Opekarske sirovine sa juga Srbije koje reprezentuju ispitivani uzorci predstavljaju značajnu sirovinsku bazu za proizvodnju različitih asortimana proizvoda, visokih estetskih i fizičkomehaničkih karakteristika. Svojstva sirovina omogućuju energetski efikasnu proizvodnju u savremenim pogonima. Sirovine se mogu smatrati kvalitetnim i sa stanovišta sve strožijih ekoloških zahteva.